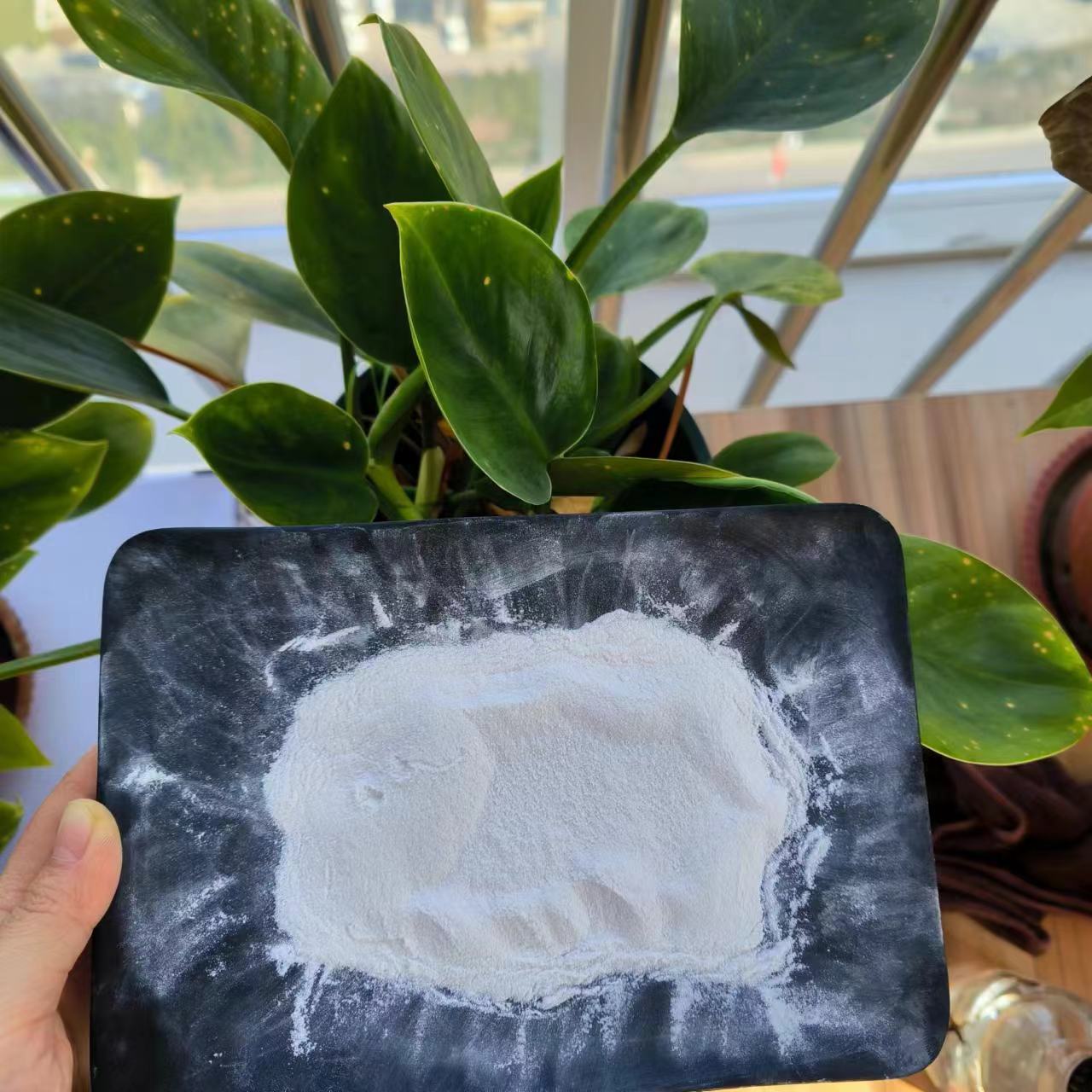
ACR用量对PVC制品表面光洁度的影响
在塑料加工领域,聚氯乙烯(PVC)凭借其成本低、机械性能良好等优点被广泛应用。然而,PVC在加工过程中存在熔体流动性差、塑化困难等问题,这对制品的表面质量产生了挑战。丙烯酸酯类加工助剂(ACR)的出现有效解决了这些问题,尤其是其用量的变化对PVC制品表面光洁度有着显著影响。
ACR能够改善PVC加工性能的原理基于其与PVC分子间的相互作用。ACR的分子结构与PVC具有一定的相似性,它可以在PVC加工过程中起到内增塑和外润滑的双重作用。ACR的加入能够促进PVC树脂的塑化,降低熔体的粘度,使PVC在加工过程中更容易流动,从而为改善表面光洁度奠定了基础。
当ACR用量较低时,虽然能在一定程度上促进PVC塑化,但作用效果有限。此时,PVC熔体的流动性改善不明显,在挤出或注塑等加工过程中,熔体难以快速、均匀地填充模具型腔。这会导致制品表面出现流痕、凹凸不平等缺陷,严重影响表面光洁度。比如在生产PVC管材时,低用量的ACR可能使管材表面粗糙,光泽度差,不仅影响美观,还可能增加流体输送时的阻力。
随着ACR用量的增加,PVC熔体的流动性得到显著改善。ACR在PVC分子链间起到了有效的润滑和分散作用,使熔体能够更顺畅地在模具中流动并均匀填充。当ACR用量达到一个适中水平时,PVC制品的表面光洁度达到最佳状态。此时,熔体能够快速且均匀地覆盖模具表面,成型后的制品表面光滑平整,具有良好的光泽度。在生产PVC板材时,适量的ACR能使板材表面如镜面般光滑,提高了产品的档次和应用范围。
然而,当ACR用量继续增加超过一定范围时,反而会对PVC制品表面光洁度产生负面影响。过多的ACR会使PVC熔体的粘性降低过度,导致熔体在模具中流动时出现“打滑”现象。这种不稳定的流动状态会使制品表面产生气泡、麻点等缺陷。此外,过量的ACR还可能在制品表面析出,形成一层薄薄的“油膜”,不仅影响表面光洁度,还可能降低制品的表面硬度和耐磨性。
除了直接影响熔体流动性外,ACR用量还会间接影响PVC制品表面光洁度。ACR用量的变化会改变PVC制品的结晶行为和微观结构。适量的ACR能使PVC结晶更加均匀、细小,有利于提高表面光洁度;而过量的ACR可能破坏PVC的结晶结构,导致表面缺陷的产生。
ACR用量对PVC制品表面光洁度有着复杂而关键的影响。在实际生产中,塑料加工企业需要根据具体的PVC制品类型、加工工艺和质量要求,通过实验精确确定ACR的最佳用量。只有这样,才能在保证生产效率的同时,生产出表面光洁度高、质量优良的PVC制品,满足市场对高品质塑料制品的需求,推动塑料加工行业的健康发展。
In the field of plastics processing, polyvinyl chloride (PVC) is widely used due to its advantages such as low cost and good mechanical properties. However, PVC suffers from poor melt fluidity and difficult plasticization during processing, which challenges the surface quality of the products. The emergence of acrylate processing aids (ACR) has effectively solved these problems, especially its dosage changes have a significant impact on the surface finish of PVC products.
The principle that ACR can improve the processing performance of PVC is based on its interaction with PVC molecules, the molecular structure of ACR has certain similarities with PVC, it can play a dual role in PVC processing of internal plasticizing and external lubrication, the addition of ACR to promote the plasticization of PVC resin, reduce the viscosity of the melt, so that PVC in the processing process is easier to flow, which provides a basis for improving the surface finish. Surface finish laid the foundation.
When the amount of ACR is low, although it can promote PVC plasticization to a certain extent, but the effect is limited. At this time, the PVC melt fluidity improvement is not obvious, in the extrusion or injection molding process, the melt is difficult to fill the mold cavity quickly and evenly. This will lead to product surface flow marks, unevenness and other defects, seriously affecting the surface finish. For example, in the production of PVC pipe, a low amount of ACR may make the pipe surface rough, poor gloss, not only affecting aesthetics, but also may increase the resistance of fluid transportation.
As the amount of ACR increases, the fluidity of the PVC melt is significantly improved. ACR plays an effective lubricating and dispersing role between the PVC molecular chains, so that the melt can flow more smoothly in the mold and evenly filled. When the amount of ACR reaches a moderate level, the surface finish of PVC products reaches an optimal state. At this time, the melt can quickly and evenly cover the mold surface, the molded product surface is smooth and flat, with good gloss. In the production of PVC sheet, the appropriate amount of ACR can make the surface of the sheet as smooth as a mirror, which improves the grade and application of the product.
However, when the ACR dosage continues to increase beyond a certain range, but will have a negative impact on the surface finish of PVC products. Too much ACR will make the PVC melt viscosity reduced excessively, resulting in melt flow in the mold when the phenomenon of “slippery”. This unstable flow state will make the product surface bubbles, pitting and other defects. In addition, excessive ACR may also precipitate on the surface of the product, forming a thin layer of “oil film”, which not only affects the surface finish, but also reduces the surface hardness and wear resistance of the product.
In addition to directly affecting the melt fluidity, ACR dosage will also indirectly affect the surface finish of PVC products. changes in the amount of ACR will change the crystallization behavior and microstructure of PVC products. The right amount of ACR can make PVC crystallization more uniform, fine, conducive to improving the surface finish; and excessive ACR may destroy the crystalline structure of PVC, resulting in the generation of surface defects.
ACR dosage has a complex and critical impact on the surface finish of PVC products. In actual production, plastics processing enterprises need to accurately determine the optimal amount of ACR through experiments according to the specific type of PVC products, processing technology and quality requirements. Only in this way can we ensure the production efficiency at the same time, produce high surface finish, excellent quality PVC products, to meet the market demand for high quality plastic products, and promote the healthy development of the plastics processing industry.
Leave a Reply
Your email address will not be published. Required fields are marked *